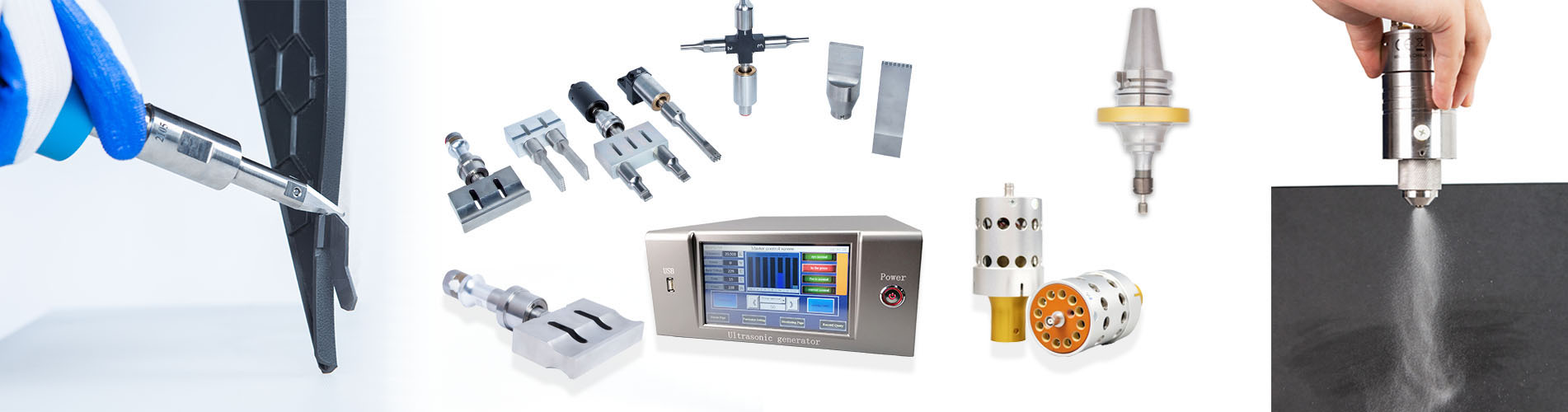
efficient way for mass production , ultrasonic welding with automation and robotics
Automatisierungsprozesse suchen kontinuierlich nach schnelleren Zykluszeiten, engeren Toleranzen des Prozesses und erhöhte Zuverlässigkeit. Vorgeladen Ultraschallschweißeinheiten sind ein weiterer Schritt, um die Grenzwerte sogar zu drücken.
Je nach den Methoden der Automatisierungsmethoden für die Massenproduktion, der flexiblen Produktion von Komponenten oder einer Kombination von mehreren Funktionen können verschiedene Technologien und Ansätze ausgewählt werden, um die Voraussetzungen zu erfüllen. Häufig verwendete Technologien sind cam-trision Systeme für einen hohen Durchsatz sowie Roboter, die wirtschaftlicher werden und neue Möglichkeiten und Bereiche von verwenden.
Die hohe Verarbeitungsgeschwindigkeit, die von Ultraschallschweißen bereitgestellt wird, macht es trotz der höheren Anfangsinvestitionen für die Massenproduktion sehr attraktiv. Während Der Prozess, die Ultraschallschwingungen, die aus der elektrischen Spannung erzeugt werden, schmelzen den Kunststoff an definierten Verbindungsstellen präzise und erzeugen ein homogenes Bonding. Zykluszeiten von bis zu 60 Zyklen pro Minute kann abhängig von den erforderlichen Schweißzeiten zwischen 80 und 450 realisiert werden Millisekunden. Die kalten Weld-Tools erfordern keine Heat-up Phase und sind jederzeit für den Betrieb bereit, ohne dass eine bestimmte Temperaturniveau aufrechterhalten wird. Gute und tiefgreifende vorläufige Anwendungsberatung ist von entscheidender Bedeutung. Dieses ist besonders für das Bauteildesign anwendbar, um das Beste möglich zu erreichen Fokussierung der Ultraschallschwingungen in den Verbindungsbereich
Vorgeladen Ultraschallschweißsysteme.
Vorlade bedeutet, dass der Zylinder bereits erweitert wurde, über ein intelligentes pneumatisches System Wann Das Schweißwerkzeug wird mit dem Material in Kontakt. Daher kann die Maschine sofort den Schweißprozess beginnen. Die in Anwendungen gespeicherte Zeit mit vielen Weld-Flecken kann sein. Der Verbinden von akustischen Schaumstoffen für ein Motorraum mit bis zu 20 Schweißflocken ist ein Beispiel, das mit anderen Robotern immer häufiger realisiert wird. In diesem Fall zeitliche Einsparungen pro Die Anwendung kann bis zu 20 Sekunden betragen.
ausführlicher ein vorgeladen Das System besteht aus einem Primärantrieb (Nocken, Servo, Roboter, usw.) und ein sekundäres, pneumatisches Antrieb. In dem sekundären Antrieb wird der Druck kontinuierlich auf den pneumatischen Zylinder des Stellglieds angelegt. Somit ist der Zylinder des Stellglieds in ausgedehntem Zustand. Der Druck im Zylinder entspricht der von der Anwendung erforderlichen Auslösekraft. Der Aktuator befindet sich in unter Druck stehender Bedingung, der aufgerufen wird "vorgeladen". Das primäre Antrieb bewegt das "vorgeladen" Aktuator in den Schweißbereich, senkt den Sonotrode auf Das Kunststoffteil, das geschweißt werden soll, um Kontakt mit der Oberfläche zu bilden und über den Kontaktpunkt des Zylinders zu fährt, so dass der Zylinderkolben des Stellglieds zurückgedrückt wird. Die resultierende Druckerhöhung im Zylinder ist entlüftet ein pneumatischer Druckregler (Präzision Druckregler oder Proportional Ventil) um den Druck im Zylinder auf einem konsistenten aufrechtzuerhalten. Anschließend mit dem Primärreisen, der seine Endposition erreicht, wird der Auslöser initiiert und der Schweißprozess ist gestartet. Der gepufferte pneumatische Zylinder führt nun die Schweißnahthubs aus. Die erforderliche Schweißkraft wird durch den pneumatischen Druckregler oder das proportionale Ventil definiert. Nach der Schweißnaht (Ende der Haltezeit) wird der gesamte Aktuator vom primären Antrieb aus dem Schweißbereich zurückbewegt. Während Dieser Reisen, der Antrieb, bewegt sich wieder auf das ausgedehnte vorgeladene Position und ist dann bereit für den nächsten Schweißzyklus.
ein Beispiel für die Verwendung von vorgeladen Systeme sind für Anwendungen mit sehr großen Mengen und wiederholten Produktion derselben oder ähnlichen Kunststoffteile, wo Schnellbetrieb Automatisierte Rotationssysteme oder lineare Transfermaschinen werden häufig verwendet. Diese Systeme arbeiten in Zeitoptimierter Zyklen; Sie sind teilweise cam-gesteuert und teilweise servogesteuert, mit Zykluszeiten einer Sekunde oder weniger pro Montage. Der Paramount-Zweck solcher Produktionssysteme besteht darin, die vollständige Zyklusreduzierung zu nutzen Potenzial bis zum letzten Millisekunden und somit, um die Teile auszugeben. WENN Ein Ultraschallschweißprozess ist integriert, alle Anforderungen an Zykluszeit müssen erfüllt sein. Der Ultraschallschweißprozess, der nur wenige Millisekunden dauert, kombiniert mit dem vorgeladen Konzept, das den Sonotrode drastisch reduziert Up / down Reisezeiten erfüllt diese Nachfrage mit hoher Zuverlässigkeit für Millionen von Teilen. Im Allgemeinen sind die Aktuatoren an einem Wagen montiert, der entweder von einem Nockenantrieb oder einem servogesteuert angetrieben wird Direktantrieb (primär Welle).
Ein weiterer typischer Setup beinhaltet automatisierte Montagesysteme Wo das vorgeladen Die Technologie verursacht die Primärwelle mit der pneumatischem vorgeladen Aktuator zum Reisen in Richtung der Schweißbereich und somit, um den pneumatischen Antriebszylinder des Aktuators zu unterdrücken. Der Ultraschallgenerator empfängt nun ein externes Triggersignal von der übergeordneten Maschinensteuerung (SPS). Sobald der Primärwellen seine Endposition erreicht, wird der Schweißprozess des Ultraschallsystems von der HU überwacht Schweißprozesssteuerung ist gestartet: Trigger-Prozess, Ultraschallschweißen, Haltezeit nach Ablauf der Haltezeit, der Hauptmaschinensteuerung (SPS) Empfängt ein fertiges Signal und bewegt die Primärwelle zurück nach Hause. Während des Zurückziehens wird der Aktuator in die vorgeladen Ende Position. WENN Es ist kein Schweißprozesscontroller verfügbar, Ultraschall-Start wird direkt vom Maschinensteuerelement ausgelöst (Zeit Verzögert).
Multi-Head Lösungen
Es ist auch möglich, mehrere Ultraschallschweißsysteme in Automatisierungsleitungen zu verwenden; Dies wird als Multi-Head bezeichnet Anwendung. Es gibt speziell entwickelte Ultraschallprodukte für Automation; Die Maschinen sind mit Frequenzen von 20, 30 und 35 kHz erhältlich und mit Ausgängen von bis zu 6,200 Watt. Es gibt sehr kompakte Designs, die meistens für Roboter-Anwendungen verwendet werden. Darüber hinaus gibt es neue Kontrollkonzepte, die leicht an die Komplexität der verschiedenen Verbindungsanwendungen angepasst werden können, und zeichnen sich durch eine einfache Integration in die Gesamtkontrolle aus.
Robotik
Die Wirkung des Schrumpfens Hochvolumen Produkte und Wachsen mehrerer Versionen von Geringten Lautstärke Produkte, insbesondere in der Automobilindustrie, haben Herstellern gezwungen, nach flexiblerer MONTAGE-Lösungen zu suchen. Heutzutage Die Anforderungen umfassen die Maximierung von Flexibilität und Bodenfläche und Minimierung der Werkzeugwechsel-Setup-Zeit. Die neuesten Entwicklungen sind flexible Ultraschallschweißzellen, die Robotik für die Montage mehrerer Kunststoffkomponenten enthalten. Dieses eliminiert die Notwendigkeit für zeitaufwändige Setup und Werkzeug ändert sich.
Eine der Hauptmerkmale dieser Montagelösungen ist Sechs-Achse Roboter. Dieses Komponente kann von jedem Robotikhersteller geliefert werden, solange der arm Last- und Schweißkräfte werden berücksichtigt, wenn Dimensionieren des Roboter.
Ein zweites Schlüsselmerkmal ist der speziell entwickelte arm arm Schweißkopf, zwei verschiedene (oben an vier) Schweißen Sonotrodes Um verschiedene Schweißvorgänge ohne Werkzeug aufzunehmen, ändern Sie sich.
Kompakte Ultraschallaktuatoren mit geringem Gewicht können leicht an Roboterarmen montiert werden und sind somit gut geeignet Fast und Niedrige Energie Verbinden von Kunststoff Teile. Vorlade Der pneumatische Zylinder des Aktuators spart Zeit - bis zu einer Sekunde pro Schweißen Spot. Dieses ist besonders in Anwendungen mit vielen Weld Spots spotbar.
Roboter werden in Situationen verwendet, wo Mehrere identische Schweißflecken müssen auf einer größeren Kunststoffkomponente durchgeführt werden. Roboterzellen bieten die höchste Flexibilität mit sehr niedrigen Zählungen und hoher Variante. Der Roboter führt jedoch die Schweißnähte Schritt für Schritt aus, was Zeit benötigt. Mit Hilfe der vorgeladen Konzept, die Sonotrode Up / down Reisezeiten können reduziert werden und die Produktivität des Roboters ist gestiegen. Trotz der reduzierten Zykluszeiten ist der erzielte Schweißprozess tadellos.
Um sicherzustellen, dass Sie wiederholt des Schweißnahtsprozesses darf der Schweißabstand nicht nur vom Roboter selbst, sondern auch von dem Aktuator zurückgeführt werden. Andernfalls würde der Roboter nach Erreichen der Schweißnahtposition müssen auf einem konsistenten Wert in den Ausgangspositionsdruck auftragen Haltezeit (Ultraschall aus). Allerdings kann das nicht Mit dem erforderlichen Präzisionsgrad realisiert werden und was ist mehr, aufwendigere Programmierung der Roboterbewegungssequenz (Position Steuerung ohne Ultraschall) würde erforderlich. Die Lösung besteht darin, die Aktuatoren immer integrieren, wenn Planung der Automatisierung Konzepte. Auf diese Weise kann ein wiederholbarer Schweißprozess sichergestellt werden während die Weichmacher und Erstarrung Phasen.
Das vorgeladen Technologie verursacht den Roboter mit der Pneumatik vorgeladen Ultraschalleinheit zum Reisen in Richtung Der Schweißbereich und somit, um den pneumatischen Antriebszylinder des Stellglieds beim Verbinden in Verbindung herzustellen. Der Ultraschallgenerator empfängt nun ein externes Triggersignal vom Roboter-Controller. Sobald die programmierten Endkoordinaten der Roboterbewegung erreicht sind, ist der Schweißprozess des Ultraschallsystems, das von der WELT-Prozesssteuerung überwacht wird, gestartet: Trigger-Prozess, Ultraschallschweißen und halten die Zeit. Nach Ablauf der Haltezeit empfängt der Roboter ein Bereitschaftssignal und hebt den Sonotrode von der Komponente um ein paar Millimeter, bevor Sie direkt zur nächsten WELT-Speake fahren. Während Die Hubphase, der Aktuator zieht sich in die vorgeladene Ende Position. WENN Es ist kein WELD-Prozesscontroller verfügbar, Ultraschall-Start wird direkt vom Robotercontroller ausgelöst (Zeit Verzögert).
Eine weitere wichtige Komponente ist ein CNC Controller, der alle Schweißprozesse und Schnittstellen mit dem Roboter steuert. Für jede Schweißnahtposition kann ein separates, optimiertes Schweißprogramm eingerichtet werden, wodurch die Möglichkeit besteht, zwischen Schweißmoden mit unterschiedlichen Kräften oder Amplituden umzuschalten und einzeln min / max Schweißnaht-Prozesssteuerung Windows.
Die Controller sind mit einem Ethernet-Anschluss ausgestattet, sodass die Schnittstelle Direkt mit Anlagennetzen oder außerhalb der Site qc Abteilungen Via Das World Wide Web für Remote Diagnostics. Dieses Ermöglicht den Benutzern auch den Überwachen und Ändern von Schweißnahtprozess-Parametern, die geschlossene Schleife bereitstellen Datenerfassung und -teile Tracking.
© Urheberrechte ©: 2025 Hangzhou Altrasonic Technology Co.,Ltd Alle Rechte vorbehalten
IPv6 Netzwerk unterstützt
Scannen an Wechat